Free-Form Facts
An OLA-sponsored article on what goes into creating digitally surfaced free-form lenses
By Alex Yoho, ABOM
In our industry, technology is taking a quantum leap right before our eyes. In the last OLA-sponsored article, "Processing Primer," we walked a job all the way through the lab pretty much as it has been since lenses were first made—rough grind, fine, and polish.
The labs of the future, however, which actually started coming into existence a few years ago, are taking advantage of computercontrolled machinery of unparalleled accuracy. Where traditional lens surfacing can achieve accuracies of around +/−0.12 diopter, these machines are accurate to 1/100th of a diopter. We are now surfacing lenses with curve variances of one millionth of a meter. What are we doing with this technology? The answer is: just about anything we want.
Yes, this technology is just squeaking past its infancy. But, with this equipment, some labs are already able to custom-surface lenses that may not be available as they were in the past—such as hyper-aspheric cataract lenses or flattop bifocals with custom slab-off in a material that may never have been available. The possibilities are boundless.
Now, manufacturing custom flattops is great, but the real beauty in this technology will be when your local lab can create the lenses that are only available from major manufacturers right now. And it won't be long.
Terms such as enhanced vision or high definition will be commonplace before you know it. But, before you use it, you've got to understand it. Just as important, you need to be able to relate the benefits to the ultimate customer.
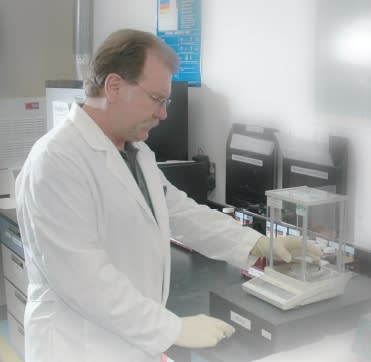
Exploring new laboratory options can result in products with higher-than-ever accuracy. Image courtesy of Transitions Optical
TECH TALK
For your technophile patients, here is a technical explanation
• SINGLE POINT. This type of surfacing differs from traditional surfacing, which basically cuts and grinds spherical curves, by pivoting the cutter on the generator around a single point. The distance from that point determines the radius of curvature and thus the power of the curve.
Angling the cutter determines the amount of cylinder or astigmatism, still around a single point of rotation.
Digital surfacing differs in that a computer controls the cutter, which is able to roam over the top of the rotating lens surface with the freedom to escape the bounds of that single point.
• POINT FILE. The distance from the cutter to the lens surface is controlled by a computer feeding the machine a "point file," so this type of machine is called a CNC generator, which stands for computer numeric control.
The information in the point file gives the machine the instructions it needs to place the cutter at somewhere upward of 10 million different points on the lens surface.
The single point diamond cutter is so sharp that it cuts the material more than grinds it, which creates an ultra-smooth surface that eliminates the traditional middle step of fining the lens before polishing. This is an important point because the nuances in curvature that address the aberrations these lenses are designed to eliminate can be broken down if they are polished too long or hard.
• POLISHING. Since these curves are not spherical, the polishing equipment is also unique. Traditional surfacing is done with hard laps that, once again, are cut around a single point allowing only round curves.
Digital surfacing is done with soft laps that conform to the unconventional curves using CNC machines that put just the right amount of polish so as not to wear away the delicate cut of the generator.

Providing patients with technical information about the production of their lenses—a compelling motivating factor in the selection of their next pair. Photos above courtesy of Santinelli International
EXPLAINING COST
That takes care of the techno geek; but what can you say to the person that asks why they are so expensive?
• MACHINERY. First of all, there is a significant increase in machinery cost. But the more ubiquitous they become, the less they will cost. At this stage, only a small percentage of a lab's work is digitally surfaced so the equipment also has to produce traditional lenses as well to help recoup the investment. Final inspection equipment is highly specialized and expensive, as well.
• FEES. To acquire the rights to use the point files to create the more exotic lenses, labs must pay "click fees" for each lens produced. This reflects the intellectual rights of the lens designer. A saving grace is that the lens blank that is created is your choice—inexpensive or a more expensive material.
The Optical Laboratories Association can be found at ola-labs.org. Check them out today. EB
WOW FACTOR | |
---|---|
What about the patient who asks, "What difference can I expect?" or "Is it worth the additional expense?" What IS the difference? The wow factor.Think of the difference between a standard and a high-definition television. This is exactly the same thing. The traditional lens, when manufactured properly, does a good job of correcting vision, but actually has quite a few aberrations (translate blur) that are perfectly normal and taken for granted.A well-designed, digitally surfaced lens eliminates these aberrations and actually widens the field of view, be it single vision or progressive. The vision is noticeably crisper and even contrast sensitivity is improved, allowing better discrimination of subtle differences of shading in darker environments. So, is it worth it? Tell patients that it's a matter of whether they are willing to settle for adequate vision or achieving dramatically improved vision and paying a bit more. |
GROWTH Plans | |
---|---|
Just as early AR coatings provided a great service to the patient, but needed improvements in durability and grew slowly, so digital lenses will grow slowly at first. The good news is that labs that process digitally surfaced lenses can check the quality of manufacture right now. As the lenses are surfaced, the power map of the lens can instantly be compared with the expected design. Finding designs that you trust will be much like finding those certain progressive lenses that you trust. When a design works in most cases, you'll probably stick with it, but try the new ones once in a while because optical design will still have some surprises for us it the near future. Since ECPs cannot measure these parameters themselves, they must rely on the integrity of the lab. Also, many of the designs are incorporating factors, such as pantoscopic tilt, face form, and vertex distance, which will yield an "as-worn" Rx. These situations will likely change as the technology develops, but for now, contact your OLA lab for the straight scoop. If they aren't digitally surfacing lenses in their own lab, they likely will have researched and work with partner labs that do. |