EQUIPMENT
Finishing School
Still not doing your own in-house edging? It’s time to take another look at finishing equipment and how it can increase customer service, profits, and even your own creativity
by Susan Tarrant
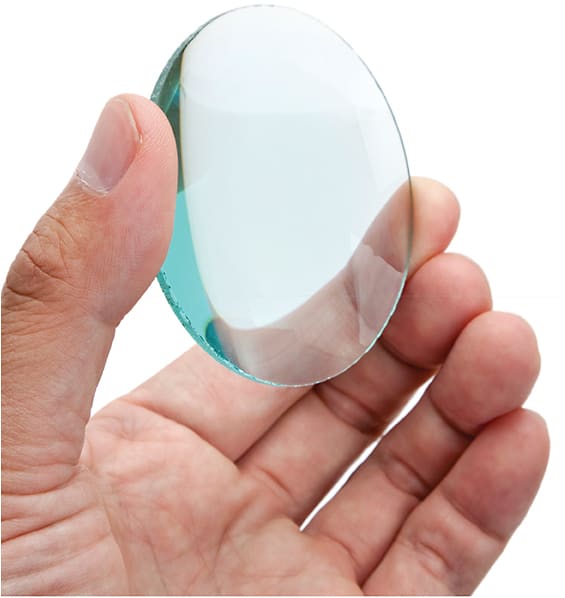
in these times of shrinking margins, in-office finishing labs have become a way for eyecare providers to better serve their patients with turnaround and quality control, and add revenue via decreased lab bills and increased business. With new responses to changing lens materials, treatments, and curves with features that can trace, block, and edge just about anything with ease in a small footprint, the time is ripe to consider in-house finishing work.
“Profits and revenues are going down in many areas of the practice, and the eyecare professional has little control over them,” says Clark Smith, eastern regional sales manager, Santinelli International. “Edging is one of the areas that you can increase your profits.”
In the Eyecare Business Annual Market Trends Study, nearly half of the responding ECPs edge their lenses in house. And they’re doing a lot of it—successfully. Twenty percent of those ECPs say they finish 75 percent of their lens jobs.
Representatives for equipment manufacturers say they hear the same refrain from ECPs who don’t edge. They don’t think they: do enough jobs, have the skill or staff, or will make any money. Following is the other side of that coin.
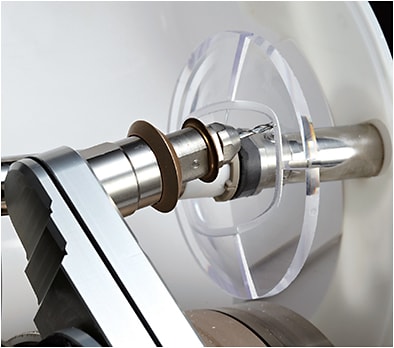
The Exxpert 8000 Finishing System from Coburn Technologies
HOT TRENDS
“Frame styles keep changing all the time, and finishing technology needs to keep up so that ECPs can continue to offer the latest styles,” explains Charlie Seidel, director of Coburn Lab Works Group, a division of Coburn Technologies. “What has really propelled in-house finishing has been the addition of easy-to-use features like drilling and specialty beveling so these new frame types can be finished in-house with shorter delivery times to customers.”
Here’s a quick look at some of the technology and features that are propelling the category.
Choose Wisely
■ BUY EQUIPMENT THAT CAN HANDLE not only what you sell now, but what you hope to sell more of in the future.
■ RESEARCH THE EQUIPMENT and the company providing it. Check online forums for referrals, talk to colleagues. Reputation is critical.
■ ASK QUESTIONS. Determine what the company will do to help your lab get started. Ask about training programs as well as service and support policies.
■ USER FRIENDLY. “For better or worse, with today’s edgers so technologically driven, you don’t need a lab rat to run the machine,” notes Carl Spear, OD, FAAO, owner of Sight and Sun Works with four locations in greater Pensacola, FL. All-in-one machines, intelligent design software, and step-by-step touch screens make the job as foolproof as possible. Little training is needed, and smaller practices can use a staff member for a couple of hours to run the jobs while larger places can hire a dedicated part-timer (or full-timer if you’re that busy) to handle the work.
■ BEVELS. A range of bevel shapes and placement options allows operators to finish lenses for any type of frame and for any Rx. Moving the bevel placement allows for a better aesthetic when fitting high-Rx lenses in frames, and varying bevel shapes mean any wrap or frame style can be accommodated.
■ DRILLING. Rimless styles have remained popular for years and show no sign of slowing. Automatic drilling technology and smart hole placement software make these styles easy. Plus, advancements such as shape modification, etching, and partial holes for inlaid gems are perfect for custom designs.
■ WRAPS. Previously the enemy of in-house tracers and edgers alike, contemporary equipment can handle just about any base curve.
■ OPTICAL TRACING. This no-touch tracing is a recent, exciting development. Available in some all-in-one systems as well as separate tracer/blockers, it uses optical digital recognition of demo lenses, allowing for a digitally accurate trace and block without inserting a frame. On-screen modification of the shape is also available.
Perhaps the biggest asset of contemporary in-house finishing equipment is the range of options available. Want something entry level that will handle simple trace and cut jobs? Or are you ready for a high-performance, high-speed system with all the bells and whistles? There really is something for all needs. Some systems even allow for mixing and matching within their lines, so ECPs can choose the tracer, blocker, and edger with the right combination of features.
“You’ve got to be willing to move up to better, faster, and more sophisticated equipment,” advises Dr. Spear. “Don’t be afraid.”
SERVICE IS KING
Sales managers out in the field say practices choose to finish in-house for two main reasons: to save money on lab bills and to increase their customer service. While the former is always desired, it’s the latter that is often cited as the real benefit.
“From a service perspective, [finishing] made absolute sense to me,” says Dr. Spear, who has been doing in-house finishing for 13 years. Located in a vacation area, a percentage of patients turn to him because they have lost or broken their eyewear and need a quick turnaround.
Jonathon Cuckler, ABOC, manager and vice president of North Colorado Optical of Greeley, Greeley, CO, says increased patient service is his main reason for finishing in house (see sidebar). It’s another layer of professionalism and service that has rewarded him through the word-of-mouth reputation his practice gets in the community.
“Do you have the kind of staff who take pride in every aspect of their job—from taking measurements to marking up lenses to fitting the finished product?” he asks. “If you do, then you can make money and serve your community better [through finishing].”
It’s Not Goodbye
Bringing finishing in house does not mean severing your relationship with your wholesale lab. ECPs will still want or need to send certain jobs out, and in most cases can buy their stock uncuts there. Most ECPs who finish in house report still sending at least 25 percent of their work out to labs.
RETURN ON INVESTMENT
It’s not difficult to Figure out the savings on wholesale lab costs versus the monthly cost of an equipment loan or lease payment plus consumables. Consider this information, provided by Briot USA (though prices noted are approximate, actual prices may vary based on lab and lens supplier).
A practice could save approximately $10 per plastic job by finishing in house ($4 stock uncut lens cost versus $14 wholesale lab edged lens cost). A polycarbonate lens could bring $15 in savings ($7 stock lens versus $22 lab cost), high-index $19($29 stock cost versus $48 from the lab), and glass $12 ($4 versus $16). A practice doing just eight jobs per day with a mixture of materials, under this analysis, could save more than $2,000 per month on lab bills. Minus a $500 or so monthly equipment payment, that’s a desirable ROI.
Profit analysis can also extend beyond the spreadsheet and include intangibles—like increased patient satisfaction, service through such things as quicker turnaround, in-house quality control, and special services like customized shapes and finishing techniques done right in the shop.
In an online survey of ECPs by Eyecare Business in September 2013, respondents reported annual profit from in-office finishing from $10,000 to six Figures.
MANAGED CARE
Vision care plans can play a role in many decisions regarding the services and products you offer, and what you charge. At least two plans prohibit or heavily restrict in-house finishing, and how much your practice or business relies on those plans will play a role in whether you invest in a lab.
“The jury is still out on how [vision plans’ restrictions] will affect the industry as a whole, but it is up to ECPs to look at the return on investment for any purchase of in-house equipment to see if it makes sense for their business,” notes Seidel. “This is something their equipment representative should be able to help them with.”
Dr. Spear suggests getting creative and find a way to work within the constraint of those few plans and make money from finishing. Computer glasses, sunwear, or any second-pair sales (that won’t go through insurance) are perfect for the in-office lab. He has even been able to convert patients to private-pay because they want the services he can offer them, such as quick turnaround.
He notes that, like everything, command of the finer points of finishing comes with time and experience. But with modern equipment, it’s easy to make a difference right away. “Those first couple of times when you are really able to take care of your patients’ needs, it’s a great feeling. Then, as you go along, you get better,” Dr. Spear recalls, adding: “Not only is it good for the patients, it’s good for your practice.”
WHY I FINISH…
Jonathon Cuckler, ABOC, manager and vice president of North Colorado Optical of Greeley, Greeley, CO, has an interesting perspective on edging. First he did it. Then he quit it.Then he did it again.
HISTORY
When he joined the practice in 2001, it had lab equipment in place. Seven years later, his business got busier, and Cuckler decided to get rid of the lab. The equipment of the day was not keeping pace with the lenses and coatings. He was encountering slippage with AR-coated lenses and software that wasn’t up for the challenge of newer lenses. He thought it best to devote the staff to patient care and eyewear sales.
However, for the next five years he was reminded what it was like to NOT handle most of the finishing himself. “After years of complaining about some of the work I was getting back, I decided to bring [the lab] back,” he says.
TODAY
Last year, he reinstated the lab with new equipment as advanced as the lens materials and treatments. It has been worth taking some of his time off the floor.
“There’s no better quality than me doing it myself,” he explains. “The money saved isn’t even the biggest issue for me; it’s the quality control and customer service.”
PRODUCT CENTER
Here is a sampling of some of the latest in-house finishing equipment releases.
AIT INDUSTRIES
A new milling feature and smart design interface sets the WECO E.6 Patternless Edger apart from its predecessor, the Edge 680. A sister product, the E.6s, brings the speed and other features of the E.6 without milling. Its C.5 blocker uses an optical tracing system, camera-assisted automated blocking, automatic drill point recognition, and a shape modification system.
INFO: aitindustries.com
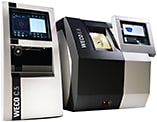
AIT Industries’ WECO E.6 Patternless Edger
BRIOT USA
The Alta Pulse is an all-material, multi-function edger for mid- to high-volume retail finishing labs. It reliably performs finishing, drilling with a variable tilt, grooving, and safety beveling, and boasts a special bevel just for curved lenses. The unit is fully versatile and can adapt to user requirements.
INFO: briot.com/usa
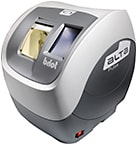
The Alta Pulse multi-function edger from Briot USA
COBURN TECHNOLOGIES
The Exxpert 8000 Finishing System (pictured on page 54) has an edger and automatic tracer/blocker—and optional drill unit. With accelerated milling technology, super hydrophobic axis twisting is eliminated, and with the optional drill unit, any lens shape or hole pattern is possible. The automatic tracer/blocker combines the functions of a tracer, lensmeter, and auto blocker in one machine. Four jobs can be processed at once.
INFO: coburntechnologies.com
ESSILOR INSTRUMENTS USA
Mr. Orange is a tracing, blocking, and edging system with a range of powerful features at a relatively modest price. Integrated functions include management of high curves up to base nine and fast optical tracing. Fit-4-Frame technology lets users determine the best lens level profile for each frame/lens combination depending on lens thickness at four strategic points. Star Control provides real-time control of cutting forces to minimize torque and stress on the lens while optimizing the speed of the edging cycle.
INFO: essilorinstrumentsusa.com
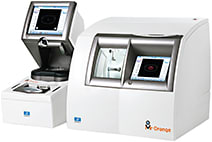
The Mr. Orange finishing system from Essilor Instruments USA
NATIONAL OPTRONICS
Precise drilling and grooving is done in one easy process with the 7Ex edger. High base lenses and complex shapes are handled proficiently with its unique cutter design. The standard cutting system includes roughing, beveling, polishing, grooving, drilling, and safety bevels along with multiple bevel designs. An optional package processes B measurements as low as 16mm.
INFO: satisloh.com
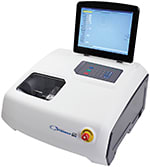
National Optronics’ 7Ex edger
OPTEK INTERNATIONAL
The Tocon ALE-5100SG is a high-speed edger with a 10.4-inch color screen. Features include multi-task job functionality and precise grooving and safety beveling. The optional rimless frame designer software allows for customized shapes. It is compatible with the FR-5000 advanced frame tracer, which features a swing function to measure high-curve frames.
INFO: optekinternational.com
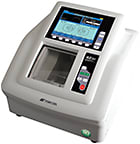
The Topcon ALE-5100SG edger from Optek International
SANTINELLI INTERNATIONAL
An all-in-one finishing solution that is compact and budget-friendly, the LE-700 Edging Station takes the operator through the tracing, blocking, edging, and grooving process via a touch display screen. Tracer-free technology measures demo lenses and patterns within the chamber. An optional front-loading frame tracer to handle high-wrap frames is available. Also, an intelligent blocker is integrated into the system.
INFO: santinelli.com
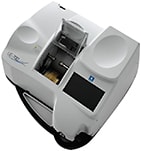
The LE-700 Edging Station from Santinelli International