5 breakthrough edging features helping in-house labs to better serve a new, more demanding customer
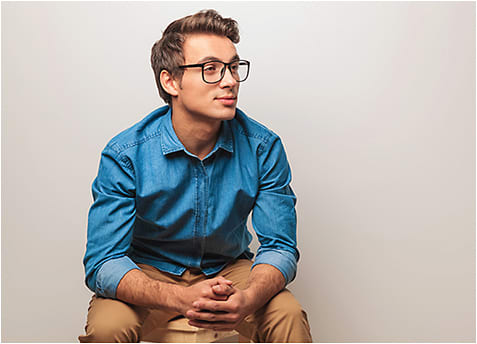
in-office finishing technology has, to coin a phrase, come a long way, baby. Besides the highly regarded advances in size and ease of use, today’s premium edging systems possess features that are uniquely suited to produce even custom jobs easily and efficiently.
Why is this important? Because it better equips ECPs to serve today’s customer who (from the millennial to boomer) seeks the fast turnaround, top-notch customer service, and personalization that an in-office finishing lab provides.
EB surveyed several edging equipment experts on the floor of Vision Expo East recently, and here’s what they say are the top five features that are helping ECPs serve today’s new customer—all with the (in most cases) literal touch of a button.
1. BEVEL CHOICES.
Sometimes, a standard V bevel in the standard spot just won’t do. Bevel features that allow the operator to choose the type and placement of the bevel allow him or her to dispense a better-looking pair of eyewear (particularly when there is lens thickness to consider) and create custom designs for high-end or high-wrap frames.
2. OPTICAL TRACING.
Most edgers of the past decade have boasted multiple-axis tracing that keeps the stylus in constant contact with the frame—regardless of base curve or shape. The next generation of this feature is the optical trace, using an optical capture of the demo lens to provide immediate shape, wrap, and (if needed) hole placement information in an instant.
The resulting benefits? Higher accuracy, better fit, easier operation.
3. CUSTOM SHAPES.
Frame-editing software—more so than any other contemporary feature—allows ECPs to cater to a customer’s desire to have custom product. Specialized milling tools take this to a whole new level, allowing intricate shapes with deep cuts (think a starburst instead of a round circle) that a cutting wheel just cannot touch.
4. LENS EMBELLISHMENT.
A sister to the shape feature is the ability to etch on or laser-engrave the lens itself. Talk about catering to customers’ sense of personalization and individualism, something on which the millennial generation puts a high value.
Customers’ initials, shapes, logos—you name it: If you can draw it, you can put it on the lens front, setting your customers’ specs apart (and bringing word-of-mouth business to your door).
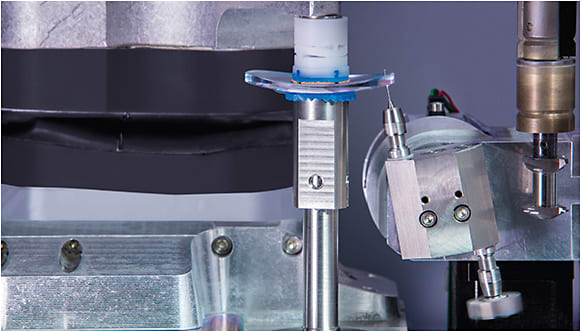
5. ONBOARD DRILLING.
Those customized three-piece mounts got much easier once drilling became automatic and brought into the edger. With no more need for a separate drill, premium machines give ECPs the freedom to find the perfect spot and angle, no matter the lens shape or material. All with one-touch operation and little risk of breakage or spoilage.
—Susan Tarrant
Bonus Points!
It’s 2017, and the industry understands the need to go green. It may not be evident to your customers, but some newer features have made edging more environmentally friendly—and that’s always a plus.
Among them is the ability to trap and dispose of swarf in a greener way, and the various filtering and vacuuming technologies that help attenuate the odor associated with edging high-index materials.