Focus on Fundamentals
There are many different coatings that can be applied to lenses. Each serves a purpose beneficial to the wearer and the lifespan of the lenses by improving lens durability, appearance, and visual performance. Different lens coatings help in various ways, from reducing glare and repelling water to protecting against scratches and harmful light. Some coatings even provide a style enhancement to lenses with a colorful mirrored finish. Understanding the fundamental benefits of lens coatings and how best to care for them will allow you as an eyecare professional to identify coating styles and characteristics and troubleshoot any performance issues.
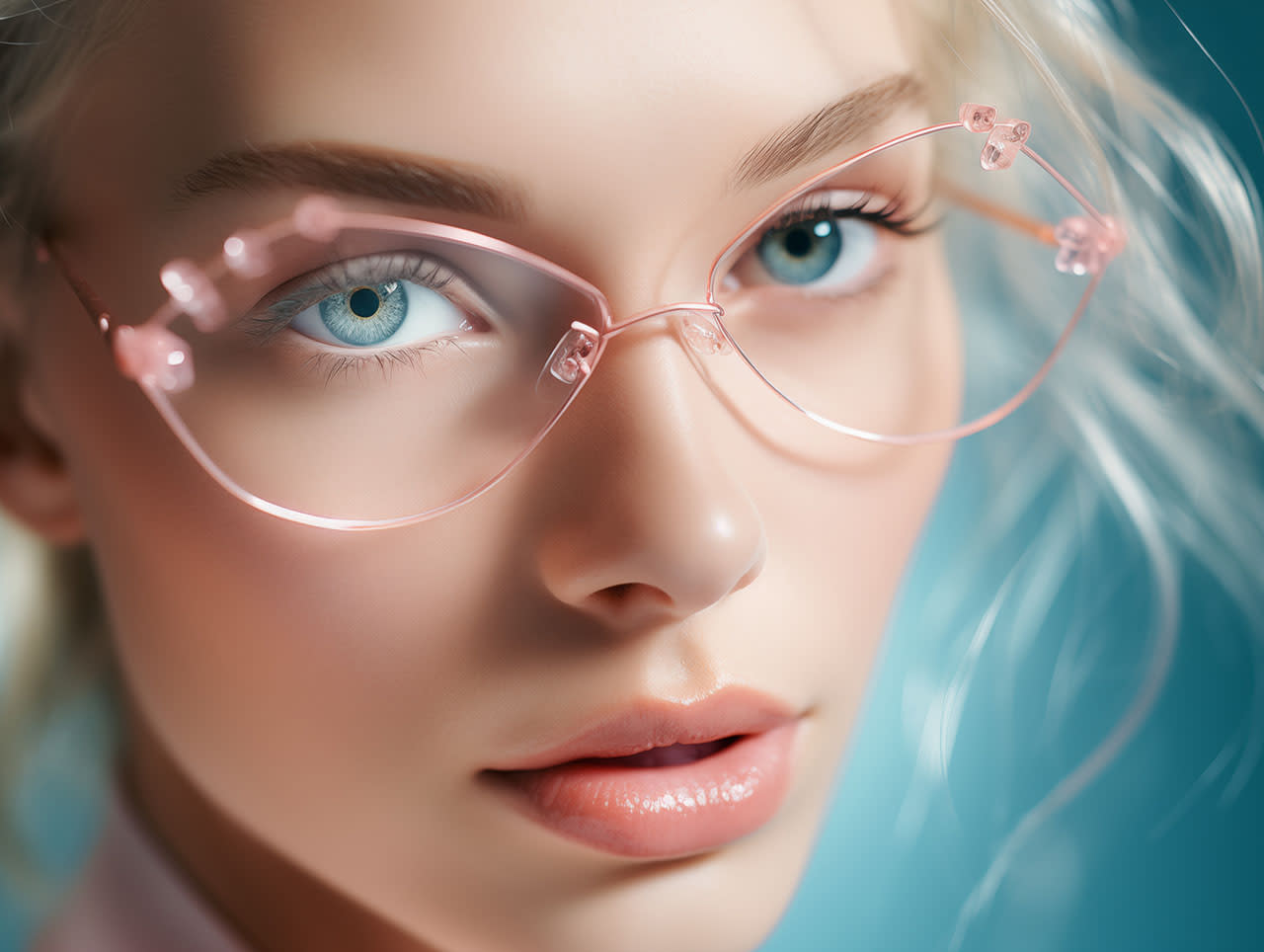
What Are Lens Coatings + Why Do We Use Them?
Lens coatings are microscopic layers of material applied to the surface of lenses to improve their functionality and longevity. Without a coating, a lens would be porous, exposed, and susceptible to scratches and discoloration, which would result in the wearer experiencing a reduction in visual acuity. Some coatings are slightly visible, whereas others are completely invisible.
Different Types of Lens Coatings
→ A scratch-resistant coating is the bare minimum of coating style that should be applied to any lens as it forms a protective layer over the surface of the lens, composed of a material harder and more resistant to abrasion than that of the lens material itself. While no coating is “scratchproof,” a scratch-resistant coating provides general protection from everyday wear and tear, making the lenses more durable and extending their lifespan. A scratch-resistant coating can be hard to identify, but it will typically have a shiny, reflective surface.
→ Anti-reflective (AR) coating should be applied to all lenses because it enhances visual clarity, improves the appearance of the lenses by making them nearly invisible, and reduces eye strain by minimizing reflection and glare and allowing more light to travel through the lens material.
When light hits a lens without an anti-reflective coating, some of it is reflected off the surface, reducing the amount of light that passes through to the eyes. AR coating uses layers of thin films with different refractive indexes. These layers cause destructive interference, which cancels out the reflections and increases light transmission, resulting in clearer, brighter vision, especially in low-light conditions.
Anti-reflective coatings are made up of multiple (and in some cases, dozens of) microscopic layers and often include a hard coat for scratch resistance, UV protection, and hydrophobic or oleophobic and antistatic layers (for more on AR coatings, click here).
An AR coating can often be identified by holding the lens to a light source; if the light reflects with a slight green, purple, or blue color to the lens surface, then the lens is treated with an AR coating.
→ Blue light coating is a special coating that filters out harmful blue light emitted by digital screens by targeting a specific wavelength of the blue light spectrum—between 380nm and 500nm, also known as high-energy visible (HEV) light. In particular, blue-violet wavelengths between 380nm and 440nm are seen as potentially damaging.
While the long-term effects of HEV blue light exposure to the eyes are not yet scientifically proven, a blue light coating can reduce eye strain and improve sleep quality, especially when worn before bedtime. Blue light coating can be easy to identify with its strong purple or blue reflective nature. Because blue light is prevalent in most settings, the coating can be especially visible on the front lens surface when exposed to a screen as it repels the HEV wavelength of light. The next installment of Focus on Fundamentals will take a more in-depth look at blue light lens applications.
→ Mirror coating is a reflective coating applied to the front surface of lenses, typically used on a sunglass lens style, tinted or polarized. Mirror coatings are available in a rainbow of colors to add both stylish and functional purpose of reflecting bright sunlight away from the eyes. The highly visible mirror-like finish is easy to identify on a lens surface, due to its iridescent and usually colorful nature.
Coating Conundrums
Lens coatings are applied to the surface of a lens, on the front, back, or both surfaces. Over time or in extreme cases of exposure, the coating can craze, chip, peel, or bubble off the lens.
The most common issue with lens coatings other than the usual wear and tear and scratching is lens crazing. This is a phenomenon that occurs when tiny, hairline cracks appear on the surface of eyeglass lenses. It can look like a spiderweb, or make the lens appear textured, crackled, or blurred when viewed at certain angles or under specific lighting. These cracks can affect both the aesthetic and functional aspects of the lenses, leading to reduced clarity for the wearer.
Causes of Lens Crazing
→ Thermal stress: Rapid changes in temperature can cause the lens material and its coatings to expand and contract at different rates, leading to the formation of cracks. For example, moving from a cold environment to a warm one or placing hot items near glasses can induce thermal stress.
→ Chemical exposure: Harsh chemicals, such as cleaning agents not designed for eyewear, can degrade lens coatings and make them more susceptible to crazing. This includes household cleaners, aerosol sprays, and some cosmetics.
→ Pressure: Improper lens mounting (lenses that are cut too large or mounted too tight in the frame) causes excessive pressure. Repetitive bending or twisting of the frame, such as taking them off with one hand or wearing them on top of the head, can lead to crazing.
→ Manufacturing defects: Occasionally, lenses may have inherent flaws from the manufacturing process that predispose them to crazing. Poor adhesion of coatings, uneven application, or a bad formula of ingredients can make lenses prone to unavoidable crazing.